Published on January 22, 2019. Written by: Mackenzie Crary
One of the synergies of combining 3D scanning with 3D printing is the ability to create physical replicas of real-world objects with true likeness to the original. In this tutorial, we are going to demonstrate the 3D scan to print process by taking a squirrel skull and making it twice the original size. The intention is to enlarge the skull so it can be examined in greater detail.
Download files and build them with your 3D printer, laser cutter, or CNC. Thingiverse is a universe of things. In this tutorial you will learn how to use Microsoft's beginner-friendly 3D modeling app 3D Builder for creating your first 3D models and professional 3D pri. Once your modeling phase is done, you may decide to print yourself or send your design to a 3D printing service. Smoothie-3D provides a simple solution and makes 3D printing a photo as easy as possible. Buying a 3d printer is easy. Learning to actually design 3D Models is where things start to get tricky. Windows vm on mac. In the past you were stuck with only one or two optio.
Let's take a closer look at what this process looks like and then look into the various applications that would benefit its use.
Video Demonstration
If you would like a condensed version of this tutorial, view the video here:
Step 1: 3D Scanning a Part for 3D Printing (Physical to Digital)
The squirrel skull measures approximately 2.25 inches, which is a relatively small object to scan. If you need to capture small objects into 3D in fine detail, in terms of getting the best resolution and accuracy, using a macro 3D scanning would be your best choice. A macro 3D scanner is designed specifically for scanning small objects.
In order to obtain the best quality results, the Metron Macro 3D scanner was used in the scanning portion of the project. FlexScan3D 3D scanning software comes with the Metron Macro 3D scanner. It captured individual 3D scans and merged them together into a complete digital 3D model.
Step 2: Preparing the Model for 3D Printing
Typically in our lab, we would use FlexScan3D for preparing the scan data for 3D printing by:
- Capturing 3D scans
- Cleaning up the scan data (post-processing)
- Converting the model into a watertight model
However, in this instance, Geomagic Design X was chosen instead for advanced post-processing the scan data.
Why use Geomagic Design X?The squirrel skull contained lots of very thin walled sections as well as small intricate holes. These features are likely too complex and unnecessary for the 3D printer to replicate. FlexScan3D has great hole filling tools and could have done a fairly decent job. When it comes to thin wall data and intricate data selection, Geomagic Design X has a more comprehensive toolset.
Instead of just filling holes, with Geomagic Design X you can build up and create new materials that were previously flat or empty in order to make a good 3D printed model. FlexScan3D does not have the ability to create more materials. In this instance, Geomagic Design X has a slight edge for post-processing this particular squirrel skull 3D model. For objects simpler than the squirrel skull, FlexScan3D would have been more than sufficient.
What is a watertight model and why do we need it?When we talk about getting a watertight mesh file for 3D printing, this means that the 3D model needs to be completely sealed. There should be no holes and all parts of the model have been connected properly to create a sealed solid.
The word 'watertight' means that if you put water inside the model, water will not leak out. Geomagic Design X and FlexScan3D software can make watertight .stl models from 3D scanner data for 3D printing.
If you don't have a watertight model, your 3D printing job will be unsuccessful. Since 3D printing sometimes can take hours to print depending on the complexity of your object, it is best to make sure your file is properly constructed before you enter into the final 3D printing stage. If you have a bad file, your 3D printing job will get messed up. Hours will be wasted and you would have to start all over again. Double-check that your file is watertight.
Step 3: 3D Printing a Replica (Digital to Physical)
We are now ready for 3D printing. Airwolf Axiom 3D printer 3D printed the model in PLA material. Built on top of Cura's open source slicing engine, Apex 3D printing software was developed exclusively for Airwolf printers and is optimized to make 3D printing a straightforward process. The software easily creates a customizable print job that allows for the most efficient printing of the skull. The 3D printer uses precise electronics that allow for accurate printing, getting the tiniest of details printed. Together, the combination produces a beautiful result that is dimensionally accurate and robust.
3D printing using Apex:- Open APEX and select your Airwolf 3D printer.
- Load your model file.
- Choose your four simple Quickprint settings (Filament, Print Quality, Print Support, and Platform Adhesion).
- Save your GCode and you're ready to print.
It is relatively simple to 3D print using the Airwolf Axiom 3D printer. It took about a little more than 10 hours to 3D print the skull using high quality settings. How do i sync controller to xbox one. It slowed down the printing process, but it would produce better results than using normal settings.
Final Results
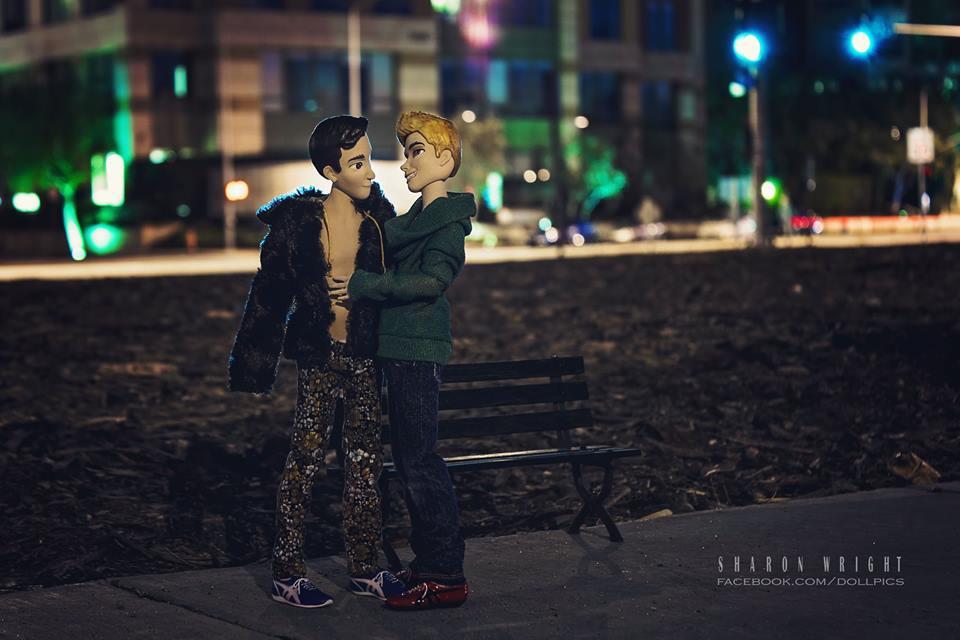
Overall, we are happy with the final 3D print. We are able to print the squirrel skull in great detail, especially around the eye socket, teeth, and the areas around the mouth. The jaw piece is also firmly attached to the model whereas the physical skull is in two pieces. The detailed model accurately represents all the features of the skull that is also robust and durable.
Applications for 3D Scanning to 3D Printing for Object Replication
Now that we gained a good understanding of the process, let's examine how this process is put into real-life uses.
- Art and Cultural Restoration Efforts
3D scanning and 3D printing can be beneficial for restoration efforts, particularly for cultural and art preservation. Precious pieces that represent our history are often destroyed with time or destruction. They require special maintenance and repair to preserve our history.
The restoration process involves scanning the remaining artifact, reconstructing the missing pieces using 3D modeling techniques, and finally recreating the missing pieces physically with 3D printing.
Case Study: Damaged Stone Sculptures Receive New Life Through 3D PrintingStep 1: 3D Scanning Step 2: 3D Modeling Step 3: 3D Printing Capturing 3D images of the authentic piece. Recreating missing fragments to create complete artifact. Sometimes, a duplicate or similar object can be used as a reference for scanning and modeling the missing pieces. Missing parts are 3D printed and adhere to the original piece to make it whole again. Funeral Busts dated back to the second century AD were severely damaged with hammers when Isis terrorists rampaged through the archaeological site and museum. The busts, one man and one woman, was taken back to Rome where cultural heritage experts from the Italian Institute of Conservation and Restoration spent time repairing the damaged bust. The restoration efforts involved using a 3D scanner to capture the shattered faces into 3D and 3D printer to print the prosthetics.
'The resin prosthetics were coated with a very fine layer of stone dust to make them blend in with the original stone. It was a great honour for us to be able to restore such extraordinary artefacts, which were so brutally damaged by Isis.'
Gisella Capponi, director of the Italian Institute for Conservation and Restoration.
The prosthetics are removable and can be replaced with the original missing piece if they were ever found.
Read more about the restorative efforts:Stone sculptures smashed by Isil in ancient city of Palmyra restored to former glory by Italian experts
- Gain a Better Understanding of Our Past
Artefacts and fossils are often fragile, irreplaceable, and priceless, which makes it impossible to be handled on a constant basis. Researchers can use 3D scanners to capture the original specimen into 3D digital form and then 3D print them for a thorough in-depth analysis.
We as humans are tactile in nature. Once an object is 3D scanned into a digital 3D model, the way we interact with a physical model is completely different than interacting with the model on screen. We can gain more insights by seeing and touching a physical tangible 3D printed model because it is often easier than looking at digital scan data.
Case Study: 3D Printing Makes Its Way Into Online CoursesAt the University of Southern Queensland, Professor Bryce Barker in the Department of Anthropology gives off-campus students the opportunity to get practical hands-on lab experience which is essential to learning the course. Students will be able to handle the 3D printed specimens in their home while getting a guided tour from the professor through online course materials to improve the way students learn. The cost of 3D printing the specimens and shipping to their homes would be much cheaper than bringing the distance and online students physically into the university (in terms of cost of travel, accommodation, etc.).
- Making Large-Scale Sculptures
The art of sculpture making can be further enhanced with the use of 3D technologies. Object replication using 3D scanning isn't just restricted to the use of a 3D printer. To expand the list of material choices for producing the final sculpture, 3D scanned data can be exported for use on a CNC machine (using wood or plastic) or for a molding process (bronze casting). Typically, artists choose to work in clay first. Once the sculpture is complete, it is 3D scanned, scaled to the appropriate size (enlarge or reduction), and produced in the finishing material.
Case Study: Making CNC-Carved Wooden Statues from Clay SculpturesStep 1: Creating the Physical Sculpture Step 2: 3D Scanning Step 3: 3D Printing, CNC, or Molding Process Sculpting the piece in clay. 3D scanning the sculpture into 3D digital form and making any necessary modifications. Produce the final sculpture in the desired materials as specified by the artist. Commissioned by the Schweizerholz (Swiss wood) initiative and the Swiss Federal Office for the Environment, figurative artist Inigo Gheyselinck created wooden figures of famous Swiss people to make history come alive and to show what a great material wood is with the #WOODVETIA campaign. The purpose of the campaign was to raise awareness of the benefits of wood, which is biodegradable and an eco-friendly material for construction and furniture production.
Gheyselinck modeled the famous heads in clay. He scanned the clay sculptures and found human models which was also 3D scanned to compose the body.
After scanning his clay sculptures using Artec Eva, the digital 3D models were then exported to CAD-compatible CNC milling machine for creating the sculpture in wood. CNC has the ability to machine soft woods at high speed.
Read more:Making CNC-carved wooden statues of historical Swiss personalities
3D scanning broadens the use of 3D printing by expanding the number of things you can do with a 3D printer. Hopefully this will give you a better understanding of the 3D print to scan process and inspire you to find more commercial applications that can benefit from the use of these technologies. Gondoliers pizza menu.
Related Articles
5 Mistakes to Avoid When Designing a 3D Model for 3D Printing
We know that modeling for 3D printing can be confusing: in 3D modeling, as in 3D printing, there is no one size fits all approach. We all use different software, print in different materials, and not only use different printers but also different printing technologies. So it's perfectly normal to feel lost and it can sometimes seem difficult to design a perfect 3D model for 3D printing.
That's why we've put together the ultimate list of mistakes to avoid when turning a 3D model into a 3D print.
1. Ignoring Material Guidelines
Each and every printing material is different. Materials can be brittle or strong, flexible or solid, smooth or rough, heavy or light, and so on. This also means that an object should ideally be designed for a specific material. For example, if you know that you want to print your 3D model in Steel, there will be specific material-related design recommendations that you need to take into account such as supporting overhanging parts, strengthening elements that are sticking out, rounding off corners, etc.
The choice of your printing material simply pre-determines some of the basic design guidelines that you need to stick to.
Each 3D printing material is different. Make sure to read the design guide for the material of your choice.
Solution: Sticking to the design rules of your material is essential for a successful print. Ideally, you should read the design guides before you start to work on your model. You can find the design guides for all of our materials here. Additionally, you can compare several materials directly on our comparison site.
How to play modern warfare 2 multiplayer free. We also encourage you to browse through our shop items (you can set a filter for specific materials there) to get a better understanding of what designs other artists have created in what materials.
2. Ignoring Printing Technology
It's not only the basic chemical characteristics of our printing materials that are different, but also the technologies that are used for printing each of these materials.
The best example of this is interlocking parts; in materials like ABS, Polyamide, Alumide, or Rubber-like you can print interlocking parts, while in others like Gold, Silver, Bronze, or Resin this is not possible. The reason behind this is not the material itself, but the technology that is used for printing each of these materials.
For ABS we use Fused Deposition Modeling (filament-based) with an extra nozzle and material for support, for Polyamide, Alumide, and Polypropylene we use Laser Sintering (powder-based), for precious metals we use lost wax casting (based on a 3D print in wax and a mold), and for the Resins we use Stereolithography (liquid polymer-based).
This might sound confusing but the important thing to keep in mind is the following: we cannot assume that Stainless Steel and Silver will have similar requirements simply because they are both metals. They are printed using different technologies and thus some design features will differ. However, materials that use the same technology such as Gold, Silver, Bronze, and Brass (lost wax casting) are more likely to share similar design requirements.
Solution: Once again, our materials website holds all the answers. Checking our material pages before you start designing is always key. Also, keep in mind that with the use of different printers and printing technologies, the maximum printing sizes differ. You can find an overview of these here.
3. Ignoring Wall Thickness
Even though you can find information about the wall thickness in the guidelines that were already mentioned, it's worth stressing this point again.
Problems linked to wall thickness are by far the most common reasons why some 3D models are not printable. In some cases, wall thickness is too thin. Walls that are too thin make small parts on the model unable to be printed or very fragile and could break off easily. In other cases, walls that are too thick generate too much internal stress and could cause the item to crack or even break.
Getting the right wall thickness is crucial for a successful print.
How To Design 3d Models For Printing
Solution: First, read our general blog post about getting the perfect wall thickness for your 3D model. Then, head over to the design guide for the material of your choice and stick to the values mentioned there.
4. Ignoring File Resolution
Read the design guides? Know your material? Wall thickness ok?
Perfect, but now there is another thing to consider: file resolution.
For 3D printing, the most common file format is STL (which stands for standard triangle language), which means that your design will be translated into triangles in a 3D space. Most 3D modeling software has the option to export your designs to an STL file and set the desired resolution.
Low-resolution STL file: It's important to be aware that a poor-quality export will never allow us to provide you with a good print. Low-resolution means that the triangles in your STL file are big and the surface of your print will not be smooth. It will lead to a somewhat 'pixelated' print.
Very high-resolution STL file: A file with a resolution that is too high will make your file too big and sometimes impossible for us to handle. It might also contain an extreme level of detail that the 3D printers simply cannot print. That's why we ask you to stay below a file size of 100 MB when uploading your model to our website.
Solution: In most 3D modeling software, when exporting a file you will be asked to define the tolerance for the export. This tolerance is defined as the maximum distance between the original shape and the STL mesh you are exporting. We advise choosing 0.01 mm for a good export.
Here's a visual representation of different file resolutions from extremely high (left) to quite low (right):
Choosing the right resolution for your file is important to ensure a good quality print.
Exporting with a tolerance smaller than 0.01 mm does not make sense because the 3D printers cannot print at this level of detail. When exporting with a tolerance larger than 0.01 mm, triangles might become visible in the 3D print. You can read more about this in our blog post about file resolution where we also point out the 40 other 3D files that we support. If your file exceeds 100 MB we can provide an offline quote if you send a zipped file via a file transfer service to contact@i.materialise.com.
5. Ignoring Software Guidelines
Our community uses many different 3D modeling software packages. Some were designed for creating 3D prints, others are mostly used by 3D artists and their designs will require additional editing before they can offer a printable 3D model. For example, applying a wall thickness is automatic in some programs, while you must manually set it in others.
Even if you use a beginner-friendly software that was developed for the sole purpose of 3D Printing (e.g. Tinkercad), you might still have a difficult time creating a hollow model. In this case, free software Meshmixer can help.
Different software, different file preparation procedures: Tinkercad (left) and Blender (right).
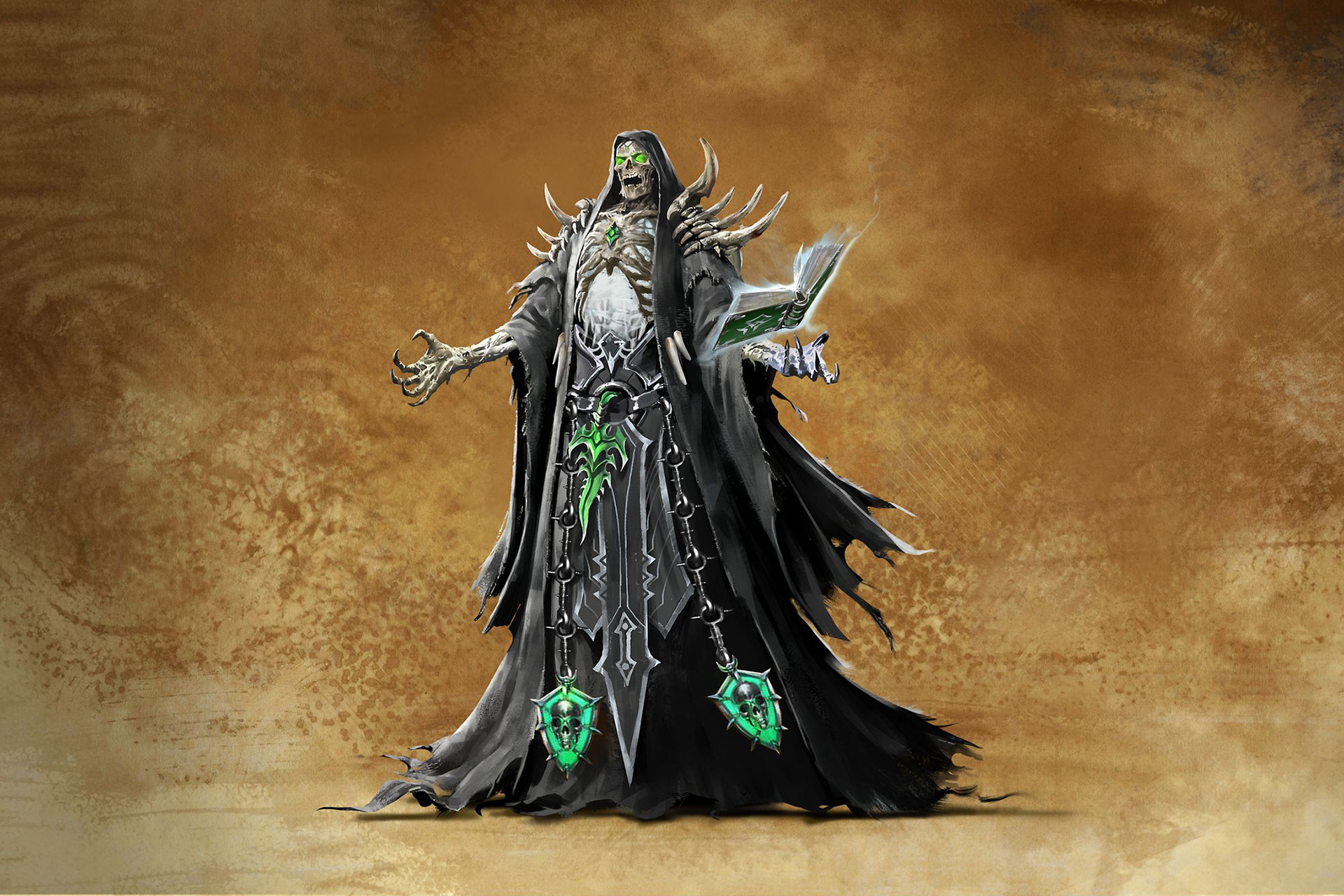
Overall, we are happy with the final 3D print. We are able to print the squirrel skull in great detail, especially around the eye socket, teeth, and the areas around the mouth. The jaw piece is also firmly attached to the model whereas the physical skull is in two pieces. The detailed model accurately represents all the features of the skull that is also robust and durable.
Applications for 3D Scanning to 3D Printing for Object Replication
Now that we gained a good understanding of the process, let's examine how this process is put into real-life uses.
- Art and Cultural Restoration Efforts
3D scanning and 3D printing can be beneficial for restoration efforts, particularly for cultural and art preservation. Precious pieces that represent our history are often destroyed with time or destruction. They require special maintenance and repair to preserve our history.
The restoration process involves scanning the remaining artifact, reconstructing the missing pieces using 3D modeling techniques, and finally recreating the missing pieces physically with 3D printing.
Case Study: Damaged Stone Sculptures Receive New Life Through 3D PrintingStep 1: 3D Scanning Step 2: 3D Modeling Step 3: 3D Printing Capturing 3D images of the authentic piece. Recreating missing fragments to create complete artifact. Sometimes, a duplicate or similar object can be used as a reference for scanning and modeling the missing pieces. Missing parts are 3D printed and adhere to the original piece to make it whole again. Funeral Busts dated back to the second century AD were severely damaged with hammers when Isis terrorists rampaged through the archaeological site and museum. The busts, one man and one woman, was taken back to Rome where cultural heritage experts from the Italian Institute of Conservation and Restoration spent time repairing the damaged bust. The restoration efforts involved using a 3D scanner to capture the shattered faces into 3D and 3D printer to print the prosthetics.
'The resin prosthetics were coated with a very fine layer of stone dust to make them blend in with the original stone. It was a great honour for us to be able to restore such extraordinary artefacts, which were so brutally damaged by Isis.'
Gisella Capponi, director of the Italian Institute for Conservation and Restoration.
The prosthetics are removable and can be replaced with the original missing piece if they were ever found.
Read more about the restorative efforts:Stone sculptures smashed by Isil in ancient city of Palmyra restored to former glory by Italian experts
- Gain a Better Understanding of Our Past
Artefacts and fossils are often fragile, irreplaceable, and priceless, which makes it impossible to be handled on a constant basis. Researchers can use 3D scanners to capture the original specimen into 3D digital form and then 3D print them for a thorough in-depth analysis.
We as humans are tactile in nature. Once an object is 3D scanned into a digital 3D model, the way we interact with a physical model is completely different than interacting with the model on screen. We can gain more insights by seeing and touching a physical tangible 3D printed model because it is often easier than looking at digital scan data.
Case Study: 3D Printing Makes Its Way Into Online CoursesAt the University of Southern Queensland, Professor Bryce Barker in the Department of Anthropology gives off-campus students the opportunity to get practical hands-on lab experience which is essential to learning the course. Students will be able to handle the 3D printed specimens in their home while getting a guided tour from the professor through online course materials to improve the way students learn. The cost of 3D printing the specimens and shipping to their homes would be much cheaper than bringing the distance and online students physically into the university (in terms of cost of travel, accommodation, etc.).
- Making Large-Scale Sculptures
The art of sculpture making can be further enhanced with the use of 3D technologies. Object replication using 3D scanning isn't just restricted to the use of a 3D printer. To expand the list of material choices for producing the final sculpture, 3D scanned data can be exported for use on a CNC machine (using wood or plastic) or for a molding process (bronze casting). Typically, artists choose to work in clay first. Once the sculpture is complete, it is 3D scanned, scaled to the appropriate size (enlarge or reduction), and produced in the finishing material.
Case Study: Making CNC-Carved Wooden Statues from Clay SculpturesStep 1: Creating the Physical Sculpture Step 2: 3D Scanning Step 3: 3D Printing, CNC, or Molding Process Sculpting the piece in clay. 3D scanning the sculpture into 3D digital form and making any necessary modifications. Produce the final sculpture in the desired materials as specified by the artist. Commissioned by the Schweizerholz (Swiss wood) initiative and the Swiss Federal Office for the Environment, figurative artist Inigo Gheyselinck created wooden figures of famous Swiss people to make history come alive and to show what a great material wood is with the #WOODVETIA campaign. The purpose of the campaign was to raise awareness of the benefits of wood, which is biodegradable and an eco-friendly material for construction and furniture production.
Gheyselinck modeled the famous heads in clay. He scanned the clay sculptures and found human models which was also 3D scanned to compose the body.
After scanning his clay sculptures using Artec Eva, the digital 3D models were then exported to CAD-compatible CNC milling machine for creating the sculpture in wood. CNC has the ability to machine soft woods at high speed.
Read more:Making CNC-carved wooden statues of historical Swiss personalities
3D scanning broadens the use of 3D printing by expanding the number of things you can do with a 3D printer. Hopefully this will give you a better understanding of the 3D print to scan process and inspire you to find more commercial applications that can benefit from the use of these technologies. Gondoliers pizza menu.
Related Articles
5 Mistakes to Avoid When Designing a 3D Model for 3D Printing
We know that modeling for 3D printing can be confusing: in 3D modeling, as in 3D printing, there is no one size fits all approach. We all use different software, print in different materials, and not only use different printers but also different printing technologies. So it's perfectly normal to feel lost and it can sometimes seem difficult to design a perfect 3D model for 3D printing.
That's why we've put together the ultimate list of mistakes to avoid when turning a 3D model into a 3D print.
1. Ignoring Material Guidelines
Each and every printing material is different. Materials can be brittle or strong, flexible or solid, smooth or rough, heavy or light, and so on. This also means that an object should ideally be designed for a specific material. For example, if you know that you want to print your 3D model in Steel, there will be specific material-related design recommendations that you need to take into account such as supporting overhanging parts, strengthening elements that are sticking out, rounding off corners, etc.
The choice of your printing material simply pre-determines some of the basic design guidelines that you need to stick to.
Each 3D printing material is different. Make sure to read the design guide for the material of your choice.
Solution: Sticking to the design rules of your material is essential for a successful print. Ideally, you should read the design guides before you start to work on your model. You can find the design guides for all of our materials here. Additionally, you can compare several materials directly on our comparison site.
How to play modern warfare 2 multiplayer free. We also encourage you to browse through our shop items (you can set a filter for specific materials there) to get a better understanding of what designs other artists have created in what materials.
2. Ignoring Printing Technology
It's not only the basic chemical characteristics of our printing materials that are different, but also the technologies that are used for printing each of these materials.
The best example of this is interlocking parts; in materials like ABS, Polyamide, Alumide, or Rubber-like you can print interlocking parts, while in others like Gold, Silver, Bronze, or Resin this is not possible. The reason behind this is not the material itself, but the technology that is used for printing each of these materials.
For ABS we use Fused Deposition Modeling (filament-based) with an extra nozzle and material for support, for Polyamide, Alumide, and Polypropylene we use Laser Sintering (powder-based), for precious metals we use lost wax casting (based on a 3D print in wax and a mold), and for the Resins we use Stereolithography (liquid polymer-based).
This might sound confusing but the important thing to keep in mind is the following: we cannot assume that Stainless Steel and Silver will have similar requirements simply because they are both metals. They are printed using different technologies and thus some design features will differ. However, materials that use the same technology such as Gold, Silver, Bronze, and Brass (lost wax casting) are more likely to share similar design requirements.
Solution: Once again, our materials website holds all the answers. Checking our material pages before you start designing is always key. Also, keep in mind that with the use of different printers and printing technologies, the maximum printing sizes differ. You can find an overview of these here.
3. Ignoring Wall Thickness
Even though you can find information about the wall thickness in the guidelines that were already mentioned, it's worth stressing this point again.
Problems linked to wall thickness are by far the most common reasons why some 3D models are not printable. In some cases, wall thickness is too thin. Walls that are too thin make small parts on the model unable to be printed or very fragile and could break off easily. In other cases, walls that are too thick generate too much internal stress and could cause the item to crack or even break.
Getting the right wall thickness is crucial for a successful print.
How To Design 3d Models For Printing
Solution: First, read our general blog post about getting the perfect wall thickness for your 3D model. Then, head over to the design guide for the material of your choice and stick to the values mentioned there.
4. Ignoring File Resolution
Read the design guides? Know your material? Wall thickness ok?
Perfect, but now there is another thing to consider: file resolution.
For 3D printing, the most common file format is STL (which stands for standard triangle language), which means that your design will be translated into triangles in a 3D space. Most 3D modeling software has the option to export your designs to an STL file and set the desired resolution.
Low-resolution STL file: It's important to be aware that a poor-quality export will never allow us to provide you with a good print. Low-resolution means that the triangles in your STL file are big and the surface of your print will not be smooth. It will lead to a somewhat 'pixelated' print.
Very high-resolution STL file: A file with a resolution that is too high will make your file too big and sometimes impossible for us to handle. It might also contain an extreme level of detail that the 3D printers simply cannot print. That's why we ask you to stay below a file size of 100 MB when uploading your model to our website.
Solution: In most 3D modeling software, when exporting a file you will be asked to define the tolerance for the export. This tolerance is defined as the maximum distance between the original shape and the STL mesh you are exporting. We advise choosing 0.01 mm for a good export.
Here's a visual representation of different file resolutions from extremely high (left) to quite low (right):
Choosing the right resolution for your file is important to ensure a good quality print.
Exporting with a tolerance smaller than 0.01 mm does not make sense because the 3D printers cannot print at this level of detail. When exporting with a tolerance larger than 0.01 mm, triangles might become visible in the 3D print. You can read more about this in our blog post about file resolution where we also point out the 40 other 3D files that we support. If your file exceeds 100 MB we can provide an offline quote if you send a zipped file via a file transfer service to contact@i.materialise.com.
5. Ignoring Software Guidelines
Our community uses many different 3D modeling software packages. Some were designed for creating 3D prints, others are mostly used by 3D artists and their designs will require additional editing before they can offer a printable 3D model. For example, applying a wall thickness is automatic in some programs, while you must manually set it in others.
Even if you use a beginner-friendly software that was developed for the sole purpose of 3D Printing (e.g. Tinkercad), you might still have a difficult time creating a hollow model. In this case, free software Meshmixer can help.
Different software, different file preparation procedures: Tinkercad (left) and Blender (right).
If you use a software like Blender (used for 3D graphics and animations), SketchUp (popular with architects and scale modelers), or ZBrush (sculpting software for 3D artists), some further file preparation will need to be done. Depending on which software you are using, shells may need to be joined together, models may need to be made watertight, wall thicknesses may need to be applied, and printing sizes may need to be set. How to photoshop using picsart. Once again, each and every software is different.
Solution: Read the software guidelines for turning a model into a 3D print. If you cannot find them on the official software websites, 'google' for tutorials. If you reach the limits of your 3D modeling software, open your 3D model in Meshmixer for some basic 3D printing preparation tools.
How To Design 3d Models For Printing Epson
Summary: How to 3D Model for Printing
Let's take a breath. And don't worry; things sound more difficult than they are. Just make sure to know your software and material of choice well. If you are struggling to learn how to 3D model you can always find a lot of resources and tutorial videos online. You can also get in touch with professional 3D designers who will be able to help you via our 3D modeling service.
If you designed a 3D model for printing, why not print it with our online 3D printing service? It's easy, fast, and efficient. When uploading a model to our website we will double-check your design manually. If there are mistakes or if parts of your object could break, we will inform you about this and tell you what went wrong. If you want to learn some other tricks, visit our blog posts about how to create stunning Multicolor + and Silver prints, how to set the perfect wall thickness, and how to choose the right file resolution.
Featured image: Spire Sculpture in Polyamide (SLS) by Charles-Eric Gogny